A South Korean worker, crushed by an industrial robot at a vegetable packaging plant, has raised serious concerns about the safety and reliability of robotic systems in industrial settings.
The incident occurred in the southern county of Goseong, where the worker, an employee of a company specializing in the installation of industrial robots, suffered fatal head and chest injuries after being grabbed and pressed against a conveyor belt by the robot's arms, as per CBS News.
Growing Concerns in Human-Robot Interaction
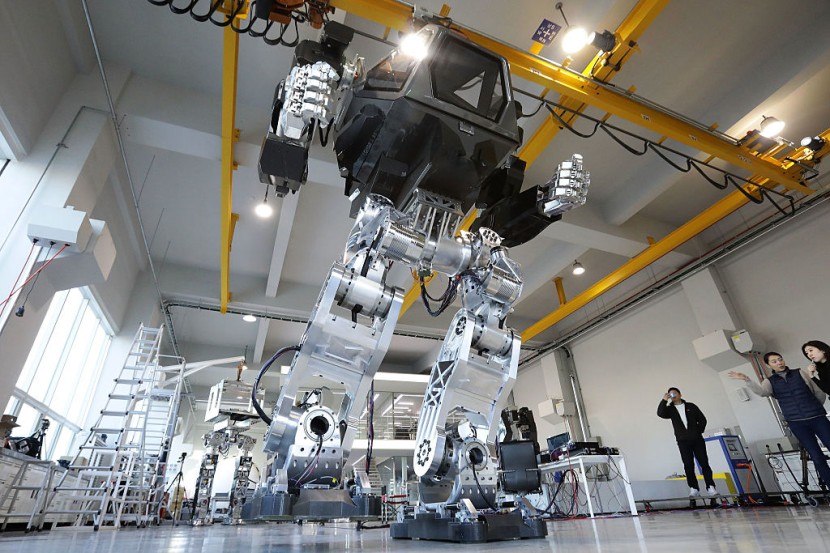
This incident highlights a growing concern in the field of industrial automation: the interaction between humans and machines, especially in environments where robots are expected to operate alongside human workers.
The worker, reportedly in his 40s, was checking the robot's sensor at a pepper sorting plant when the robot, designed to lift boxes of peppers onto pallets, malfunctioned and mistakenly identified the man as a box of vegetables.
Such accidents are not isolated incidents. In May, another worker in South Korea was seriously injured in a similar accident involving a robot at an automobile parts manufacturing plant. Data from the American Journal of Industrial Medicine shows that between 1992 and 2017, at least 41 people in the United States were killed by industrial robots, with stationary robots accounting for 83% of these fatal incidents.
A notable case occurred in 2015 when a robot killed a 22-year-old worker at a German Volkswagen factory. In the recent South Korean incident, the victim had been sent to the plant to examine whether the machine was functioning correctly.
Early evidence suggests that human error may have played a role in the accident, as the robot's sensors, designed to detect boxes, had identified the box the victim was carrying before the fatal encounter.
This accident adds to a series of similar occurrences in South Korea involving robots in factory settings. In March, a worker was crushed and seriously injured by a robot at an auto parts factory in Gunsan, and last year, a worker at a milk factory in Pyeongtaek was fatally crushed by a robot installed near a conveyor belt, according to Independent.
Robot Tragedy Spurs Safety Concerns
The robot involved in the Goseong incident was one of two pick-and-place machines used at the facility, which packages bell peppers and other vegetables for export. According to Kang Jin-gi, who heads the investigations department at Gosong Police Station, the robot was not a sophisticated AI-powered machine but a simpler device designed for repetitive tasks like box handling.
The police are working with related agencies to determine if the machine has technical defects or safety issues. The incident has prompted calls for more precise and safe systems to be established, particularly in light of South Korea's heavy reliance on industrial robots.
According to the International Federation of Robotics, the country had the highest density of industrial robots per 10,000 employees in the world in 2021. This increased adoption rate reflects the country's efforts to automate major manufacturing sectors, such as electronics and auto-making, in response to a declining aging workforce.
As robotic technology advances and increasingly integrates into various industries, the need for rigorous safety standards and protocols becomes more apparent.
This tragic event is a stark reminder of the potential risks associated with the growing use of robots in industrial settings. It underscores the importance of ensuring these machines are safe, and reliable, and distinguish between inanimate objects and human workers, Mail Online reported.
© 2025 HNGN, All rights reserved. Do not reproduce without permission.