Space Forge has developed a satellite reentry system that will allow for the quick recovery and reuse of its in-space manufacturing spacecraft.
The ForgeStar
It includes a heat shield and a water vehicle designed to soften the landing of the spacecraft, which will be added to the company's in-space manufacturing satellite platform called ForgeStar.
According to Space Forge, it built its Pridwen heat shield big enough to radiate away the heat generated by atmospheric reentry. It is made out of a high-temperature alloy and can fold inside the launcher for lift-off and unfold when the spacecraft makes its return to Earth.
They also developed an uncrewed water vehicle called the Fielder, which will maneuver itself under ForgeStar and catch it in a soft landing, as reported by TechCrunch.
This will help reduce stress on sensitive payloads inside the vehicle. At the same time, it will reduce the need for spacecraft refurbishment.
The company is among the many trying to be one of the first to exploit the potential astronomical market for materials made in space.
Space Forge is on track to launch its inaugural mission this year. However, it won't carry customer payloads; instead, it will demonstrate the company's manufacturing technique and prove its key technologies.
Space Forge, a UK-based space technology company, has developed a 3D printing technology to manufacture high-performance metal components in microgravity conditions. The technology called the Flux Core Welding (FCW) process, uses a wire-based additive manufacturing technique, which can produce intricate metal components in difficult-to-manufacture alloys. The company is set to launch its inaugural mission this year to demonstrate the technology and prove its key technologies. It is one of several companies trying to exploit the market potential for space-made materials.
Read also : SpaceX next mission: Pro-creation in space
Manufacturing in Space
The potential for manufacturing in space is vast, as microgravity conditions allow for creating materials and components that are impossible to produce on Earth.
Space Forge's FCW process offers a unique solution to this challenge by using wire-based additive manufacturing techniques to create intricate metal parts with high-performance properties.
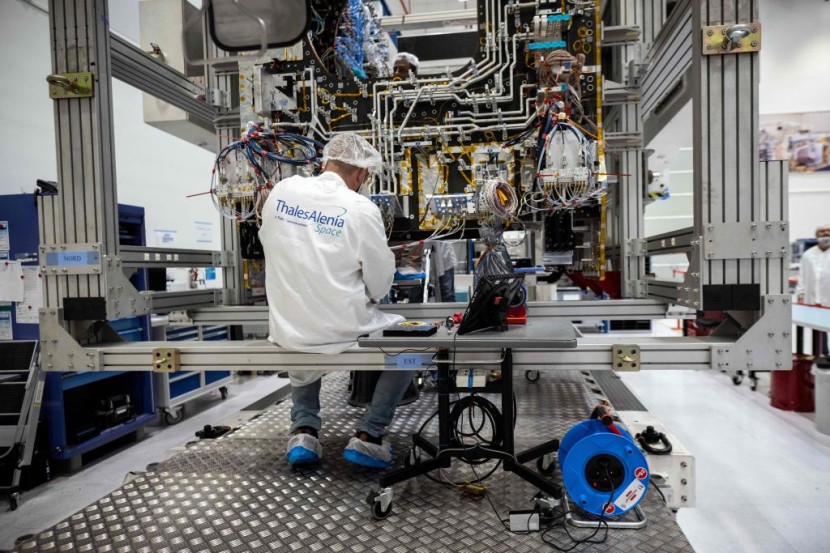
Beyond reducing stress on sensitive payloads and decreasing spacecraft refurbishment needs, the ability to manufacture in space also has significant implications for industries such as aerospace, defense, energy production, and even medicine. The development of new alloys and advanced materials could lead to stronger yet lighter structures or more efficient power systems.
As companies like Space Forge continue their work towards successful missions demonstrating these technologies' viability in orbit, it remains clear that innovation will be essential if we want humanity's expansion into space beyond mere exploration.
With pioneering advancements like 3D printing technology taking place today - which have already shown great promise both here on earth but also out there among stars- one thing seems certain: our future holds limitless possibilities!
Related article: Space Catapult Slingshots Rockets at Supersonic Speed Instead of Using Solid Fuel Boosters to Send Spacecraft to Orbit
© 2025 HNGN, All rights reserved. Do not reproduce without permission.