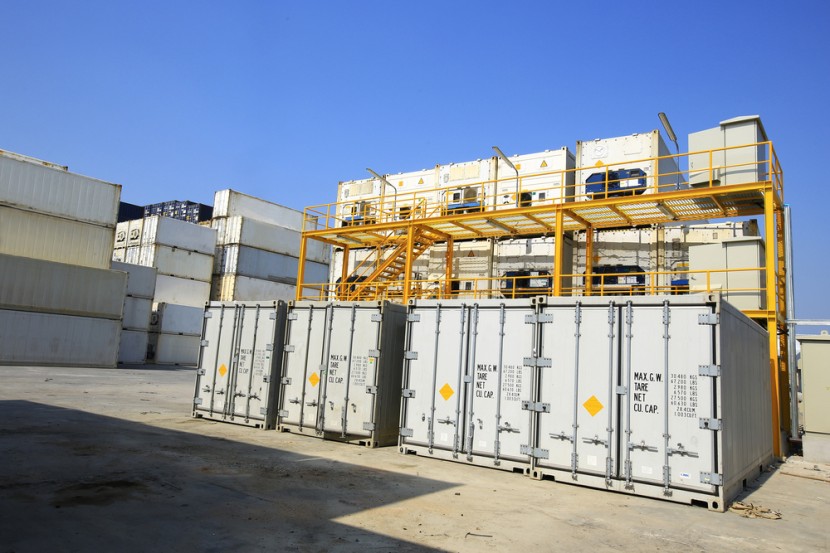
Cold chains have become even more important as the world deals with the coronavirus pandemic. More and more consumers now prefer to buy their essentials online rather than through physical stores. Delivering goods such as food, pharmaceutical goods, and medication to consumers requires the use of temperature-controlled transportation and storage facilities.
But despite the improvements in cold chain technologies such as more efficient refrigeration and integrated tracking systems, waste is still a major concern in the field. About 30 percent of the food produced for consumption globally is lost or wasted somewhere along the supply chain. The pharmaceutical industry also suffers from such issues. In the biopharma sector alone, $35 billion is lost due to cold chain failures.
To cut back on waste, industries are now actually looking into better cold chain monitoring technology to help them track the condition of each package and shipment that they handle. Through better data analytics, it is possible to identify the root causes and implement better strategies on how to minimize waste.
What Causes Waste
There is a wide range of factors that can affect shipping conditions in supply chains. Since they deal with temperature-sensitive goods, cold chains are most concerned about temperature excursions. Most of these goods have to be kept within specific temperature ranges to ensure freshness or effectiveness.
Temperature excursions are often caused by delays during transportation. Air traffic can also stall cargo airplanes, increasing the risk of cargo being subjected to adverse conditions while waiting on the runway. Likewise, city traffic can hold up delivery vans and trucks, creating similar risks of excursions.
Logistics personnel can also mishandle these products. Rough handling can damage packaging insulation that help keep the products within the recommended temperature ranges. Exposure to air, light, and even shocks and bumps can also degrade product quality. Shippers themselves can be to blame for these kinds of mishandling.
Many countries also have strict health and safety regulations that require sensitive products that suffer from temperature excursions to be discarded and disposed thus leading to waste.
How Cold Chain Monitoring Tech Works
Cold chains need to track if temperature excursions do occur and identify which of these events cause the incidents. Monitoring technology helps in this regard. Tags and tracking devices are now available that can accurately track the conditions to which any particular shipment is exposed.
These devices are equipped with sensors that can log information such as temperature, humidity, ambient light, location, and even bumps and shocks. These are also small enough to be placed on individual packages for greater accuracy. The logged information can readily be scanned and sent online, allowing shippers to quickly check if any of their packages encounter any incidents.
Cloud-based dashboards can be made accessible throughout the cold chain network. This way, all those involved can have better visibility and transparency of the condition of each package moving through the chain.
What Improvements Data Monitoring Can Bring
Having such comprehensive and accurate information can greatly help monitoring. Data can be analyzed to see at which points of their journey packages are likely to encounter incidents. The variety of data that can be gathered can even aid in pinpointing the specific causes of incidents.
Should temperature excursions be detected, shippers can immediately recall the affected packages, minimizing the potential harm of getting questionable products out in the open market. It can be cheaper and less complicated to recall products while in the middle of the chain rather than at the end. Since they can now have data recorded on individual packages, they can further isolate affected and not be forced to discard whole shipments or batches.
Condition data can also help in overall strategies such as designing better packages to ensure safe handling and even plot better transport routes to minimize delays. The information can even be used to allow for better transparency and accountability among stakeholders. Partners, personnel, facilities, and equipment that are identified to cause issues can be removed or replaced in order to build a more robust chain.
How It Benefits Stakeholders
Ultimately, effective and efficient cold chains can benefit all stakeholders. Consumers get to enjoy safer products. Spoiled food and medication can become health hazards and even spark public health crises. By ensuring that products are kept within optimal conditions, the probability of these happening can be minimized.
Less waste is also beneficial for everyone. Companies can get to save not only on the losses of the damaged goods but also on the costs that come with dealing with recalls and disposals. Consumers can even get to benefit as an abundance of supply means food and medication can be readily available to them. The companies' savings from less waste can also be passed on to consumers in the form of cheaper prices.
© 2025 HNGN, All rights reserved. Do not reproduce without permission.