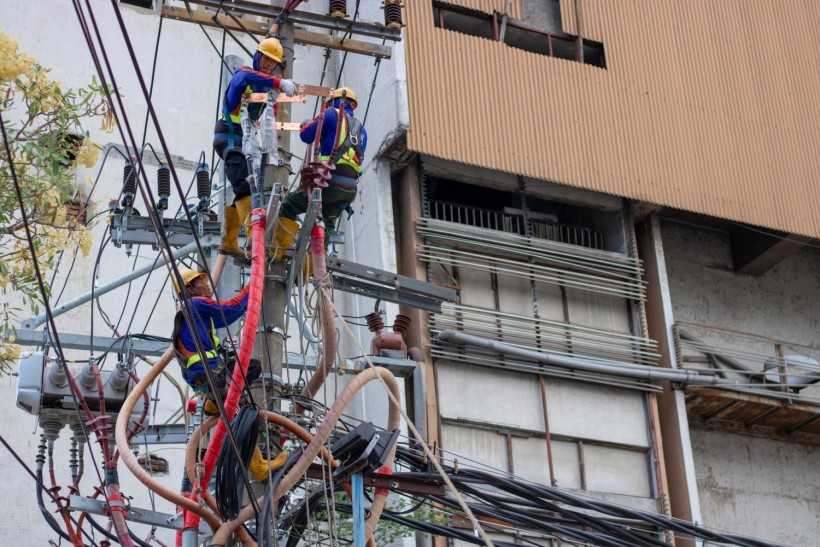
(Photo : Hobi Industri via Unsplash)
Facility maintenance refers to measurable and visible practices designed to protect and maintain a facility and its assets. Facility maintenance encompasses a broad range of activities, from renewal and renovation projects to basic maintenance tasks, including patching cracks in interior walls, painting floors, repairing small roof leakages, setting up chairs for conferences, pump cleaning tanks, and pipes, maintaining grounds of parks and schools.
To ensure that your facility is well maintained, the facility manager should put in place factors that reduce the cost of operations and increase their efficiency.
(Photo: Los Muertos Crew via Pexels)
Some of these factors include having a Facility Maintenance Plan Template that allows you to have a central place where all facility information is kept, preventing breakdowns by putting in place a preventive maintenance strategy, seeking service of professional technicians with the right technology and also educating your employees and tenants on the basic maintenance skills.
To be successful in the facility maintenance field, one should be able to understand the type of facility maintenance are areas where they are applied as described below;
Preventive Maintenance
This type of maintenance aims at preventing the problem before it even happens. This is done regularly within a specified period of the year when the inspection is carried out. During the inspection, technicians correct the damage or raise the issue to the intended person before they intensify, leading to total breakdown or unplanned system shutdown. It is also cheaper to fix an issue at this stage than during breakdown.
Reactive/Corrective Maintenance
Reactive maintenance is a common maintenance task because they are part of daily routine checking. E.g., fixing a light bulb, draining blocked sewage, repairs of the HVAC system are unforeseen and are prone to happen at any given time. This facility maintenance routine is a vicious cycle. It does not just stop there.
On the other hand, corrective maintenance is when a technician identifies an issue while undertaking another task. After identifying the problem, the technician will fix a date to come to fix the problem.
With corrective maintenance, a problem is identified therefore enabling early fixing before the damage advances.
Predictive Maintenance
With predictive maintenance, a system is monitored via a sensor device and is attached to the system software to provide real-time notification and constant feedback.
Predictive maintenance enables the technicians to be on alert as they can get a notification in danger.
This type of maintenance is highly advanced because it requires skilled personnel to interpret its data. It's recommended to keep the sensor devices in check frequently to ensure they are functioning effectively.
Predetermined Maintenance
These are suggestions that come from the manufacturer after acquiring enough data through research and also experimenting.
The manufacturer attaches a user guideline on how to use, maintain, and replace.
You may still require regular checkups by technicians, as the manufacturer's recommendations are based on research, which can differ from the functioning of a facility system.
To ensure that facility maintenance is carried out correctly, the service of a qualified industrial technician is required.
Here are some industrial maintenance jobs you should consider pursuing if you are looking forward to choosing a career in this line
Industrial Maintenance Careers
1. Production Supervisor
They are responsible for managing the production and its workers and coordinating tasks to ensure everything runs smoothly. Apart from overseeing other staff, the production supervisor should also know about machinery repair and basic safety precaution skills while working in the production area. They are also required to be on their protective gear.
2. Plant Electricians
According to the Bureau of labor statistics, plant electricians should be responsible for installation, maintenance, wiring, and lighting in an industrial.
They are also in charge of inspection and rectifying possible electric defaults. They should follow the required government policies during installation and maintenance.
(Photo: Edvin Johansson via Unsplash)
3. Machine Operators
Machinery operators use machinery to produce their instruments. They need to be knowledgeable in machinery procedure, math, metalwork, and mechanical services to carry out these duties. When undertaking their duties, they need to put on protective gear, safety glasses, hardhat, protective shoes, etc.
4. Heavy Machinery Mechanic
They are responsible for assembling machinery and equipment, repairing damaged parts, carrying out a test to identify a problem. They also perform preventive machinery maintenance.
Heavy machinery mechanics should possess various qualifications, e.g., mechanical, electrical, fabrication, and computer skills. They should be able to read through manuals and understand the equipment's functionality well. They should always put on hard hats, steel-toed shoes, safety glasses, etc.
5. Hydraulic Technician
Hydraulic technicians are responsible for installing, maintaining, and repairing machinery that uses hydraulic technology. They are required to use computers and other technology to carry out preventive maintenance. They are also tasked with diagnosing and repairing machinery within this category.
They should put on hard hats, metal-toed shoes, protective glasses, and gloves to protect themselves.
* This is a contributed article and this content does not necessarily represent the views of hngn.com